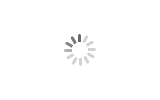
- Gaea
- China
The "Liaoning Gaea" CO2 rock demolition system offers a cutting-edge, non-explosive rock breaking technique, ideal for urban and sensitive environments. Utilizing supercritical carbon dioxide, it fractures rocks with precision and safety, minimizing vibrations and environmental impact. This innovative system provides a reliable alternative to traditional blasting methods, ensuring efficiency and eco-friendliness in construction and mining operations.
CO2 rock demolition system rock blasting tools no explosive demolition
Related reports:
How to determine the diameter of the blasting hole;
Application of Smooth Blasting Technology in Tunneling of Coal Mine;
The Gaea CO2 blasting rock system, which involves the use of specialized tubes filled with carbon dioxide that are detonated to break rock or concrete, presents a unique alternative to traditional explosives. Here are the key points you mentioned as well as some additional considerations:
Safety:
The system is considered safe in terms of fire risk since the combustion occurs within a sealed tube, and the rapid release of gas has a cooling effect that reduces the risk of igniting any gas/air mixture present.
It can be used near underground service lines without causing damage.
Classification and Reusability:
The system is not classified as an explosive but as a high-pressure gas generator, which eases regulatory restrictions.
Components like the chemical energizer, rupture disk, gasket, and the CO2 itself are replaceable, allowing the tubes to be reused multiple times, which is cost-effective and reduces the need for carrying a large stock of consumable cartridges.
Logistics and Use:
All tubes require a 57mm diameter hole, which limits flexibility in hole sizing and may not be efficient for hand drilling.
The requirement for standard hole size also means little tolerance for variation in hole diameter.
The positioning of the discharge points within the cartridge needs to be considered since they are not located at the end of the tube.
Recovery of the tubes for reuse must be factored into the project cycle, which could affect logistics on smaller projects.
Performance:
The system is reported to provide good fragmentation, breaking rock into large, manageable pieces with minimal generation of fine debris.
It is particularly effective in environments like shaft sinking where there is no free face, and it produces very little noise or vibration, which is advantageous in sensitive areas.
Applications:
Rock and concrete breakage
Deep sea excavation
Tunnelling and shaft sinking
Trenching and excavation
Quarry blasting
Clearing blockages in silos and bins
Considerations:
The cost and availability of the system components, including the chemical energizer, rupture disks, and gaskets.
Training and competency of personnel in using the system, considering its specialized nature.
Environmental impact, particularly the potential release of CO2, which is a greenhouse gas, although it might be relatively small compared to other methods.
It seems that the Gaea CO2 blasting rock system is a specialized tool that offers a balance of safety, efficiency, and environmental consideration for certain rock and concrete demolition applications. Users will need to weigh these benefits against the system's limitations and requirements to determine its suitability for specific projects.
Operation introduce:
Certainly! Let's describe the 6-step CO2 rock blasting process, ensuring each step is clearly represented:
1.Drill Holes:
Technicians start by carefully drilling holes into the rock formation according to a strategic layout that is optimized for the particular job. The holes have a diameter of 130-140mm and a depth of 6-8m, which may vary based on the construction requirements and the geology of the rock. Proper drilling ensures that the CO2 can be effectively distributed within the rock structure.
2.Fill with Carbon Dioxide:
Once the holes are drilled, a carbon dioxide filling system is used to inject liquid carbon dioxide into the rock-breaking steel pipes. The CO2 is pressurized to the point where it's in a supercritical state, meaning it exhibits properties of both liquids and gases above its critical temperature and pressure. This high-pressure CO2 will help fracture the rock when released.
3.Put the Pipes into the Holes:
With the CO2 loaded into the rock-breaking steel pipes, an excavator or other heavy machinery lifts and carefully positions each pipe at the bottom of the pre-drilled holes. It's crucial that the pipes are placed accurately to ensure the CO2 can exert maximum pressure on the rock walls.
4.Plug the Holes:
To contain the pressure of the expanding CO2, workers plug the holes with soil, gravel, or another suitable material. The quality of the plug is directly related to the blasting effect; a tighter seal will ensure that the pressure builds up sufficiently to crack the rock instead of escaping through the hole.
5.Connect the Wires:
Electrical wires are connected to the system, either in parallel or in series, depending on the specific setup and requirements. These wires are crucial for the controlled release of the CO2 and may be connected to a trigger mechanism that will initiate the blast at the appropriate time.
6.Detonate:
The final step is to detonate or release the CO2 into the rock formation. The main line is connected to a detonator or control system that triggers the rapid expansion of the supercritical CO2. The sudden increase in pressure fractures the rock, completing the rock blasting process without the use of traditional explosives.
Each step in this process is critical to the success of the CO2 rock blasting technique. Proper execution can lead to efficient rock breaking with potentially less environmental impact and vibration compared to conventional methods. Safety protocols must be strictly adhered to throughout the process to protect the workers and the environment.