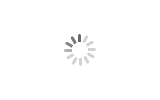
- Gaea
- China
- 5 days
- 1000pcs/month
Gaea rock is the professional shank adapter manufacturer.
including Atlas,sandvik,fukukawa,and so on.threaded including T38 T45 T51
T45 COP1238 575mm shank adapter rock drill tools
Related reports:
What are the classifications and styles of shank adapter;
The purpose and scope of application of shank adapter;
Introducing T45 COP1238 575mm Shank Adapter for Rock Drilling:
The T45 COP1238 575mm shank adapter. This shank adapter is specifically designed for rock drilling operations and is recognized for its outstanding quality, durability, and performance.
The T45 COP1238 575mm shank adapter combines the T45 thread, a widely accepted thread type in the industry, with a length of 575mm. This thread design ensures a secure and reliable connection between the shank adapter and the rock drilling machine, enabling efficient power transmission during drilling operations. The COP1238 designation further specifies the model of the shank adapter, providing compatibility and performance assurance.
Our shank adapter manufacturing process includes advanced heat treatment techniques, resulting in superior quality and enhanced performance. This heat treatment process enhances the hardness, strength, and wear resistance of the shank adapter, allowing it to withstand the demanding conditions encountered during rock drilling operations. By implementing this state-of-the-art technique, we ensure that the T45 COP1238 575mm shank adapter maintains its integrity, reduces the need for frequent replacements, and minimizes downtime.
The shank adapter, also known as a shank adaptor, is a crucial component within the drill string assembly. It plays a vital role in efficiently transferring the impact energy from the drill rig's piston to the drill string with minimal energy loss. Additionally, the shank adapter must withstand high levels of rotational torque during drilling operations. Therefore, it is imperative that the shank adapter exhibits exceptional performance, reliability, and durability.
Our T45 COP1238 575mm shank adapter is specifically engineered to meet these demanding requirements. It is designed to endure the continuous impacts from the piston, averaging 6,300 strokes per minute, while maintaining high reliability and durability. This ensures optimal performance and productivity during rock drilling operations.
Furthermore, our shank adapters are compatible with a wide range of drilling machines, including Sandvik Tamrock, Atlas Copco, Furukawa, and Ingersoll-Rand. This broad compatibility allows for seamless integration with various drilling rigs, ensuring versatility and flexibility for different drilling applications.
In summary, the T45 COP1238 575mm shank adapter offered by Liaoning Gaea is a premium product designed for rock drilling operations. Its T45 thread, precise manufacturing, and advanced heat treatment process ensure exceptional quality, durability, and performance. With compatibility across renowned drilling machine brands, our shank adapter provides a reliable and efficient solution for your rock drilling needs. Choose the T45 COP1238 575mm shank adapter from Liaoning Gaea for outstanding performance and durability in your drilling operations.
This is the specification:
Background technique:
The shank adapter is the transmission connection part between the rock drill and the threaded rock drill rod (drill rod), English shank\shank adapter. It is also one of the consumables scrapped at the rock drilling site. At present, the basic manufacturing process of shank adapter at home and abroad is divided into bar direct processing method and forging processing method.
Drilling tool steel is divided into: medium and high carbon drill steel, such as 55SiMnMo, 40CrNiMo, etc. The heat treatment method is oil quenching or air cooling after heating. Low-carbon drill steels, such as 23CrNi3Mo (EN40B), 25Cr3MnMo (SANBAR 23), 22SiMnCr2NiMo (FF710), etc., are heat treated by oil quenching after carburizing or air cooling after carburizing.
A: The processing steps of the bar direct processing method are:
A: select the corresponding drill steel; b: select the appropriate diameter and length specification; c: the shape of the machined drill shank (including splines and threads); d: select the corresponding heat treatment process according to the drill steel; e : Shot blasting and straightening treatment; f: Use cylindrical grinder to grind the middle part of the shank to the size of the drawing, (grind both ends of the plane); g: pass the inspection, apply anti-rust oil, and pack into the finished product warehouse.
B: The forging process steps are: a: select the corresponding drill steel; b: the appropriate weight of the blank; c: the shape of the forged shank and annealing treatment; d: the shape of the machined shank (including splines and threads) ; E: Select the corresponding heat treatment process according to the steel of the drill tool; f: shot blasting and straightening treatment; g: on the cylindrical grinder, grinding the middle part of the drill tail to the drawing size, (grinding the two ends of the plane); h: inspection Qualified, apply anti-rust oil, package into finished product warehouse.
The characteristics of the production process of these processing methods are: A, steel machining is completed (length, thread, spline); B, overall heat treatment in the heat treatment furnace; C, after heat treatment, shot blasting, straightening, and grinding; D, final inspection Qualified, coated with anti-rust oil, packed into finished product warehouse.
The disadvantages of these processing methods are: 1. Treat the shank as an integral part; 2. The length and thread type of the shank adapter must be determined before heat treatment, and cannot be changed after heat treatment. The product production process is too rigid and lacks flexibility; 3. The use of shank adapter is scrapped and damaged, 85% of which occurs at the threaded end. Take the common HL710 rock drill T45-600 shank adapter as an example, the length of the vulnerable part of the threaded end is about 120, accounting for 20% of the total length. It can be seen that 80% of the length of the shank adapter is over-processed by heat treatment, and comprehensively, at least 70% of the length of the shank is over-processed by heat treatment.